Flue gas heat exchangers
- Mainly for recuperation of flue gas with dust particles
- Most commonly used for thermal energy recovery in foundries, welding shops and glassworks
- Power series from 100 kW to 1 MW
- Usually delivered as a part of a technological unit
Flue Gas Heat Exchangers
Pipe heat exchanger is designed for flue-gas heat exchange with high proportion of dust particles. It is most commonly used for exchanging thermal energy from aluminum-melting furnaces, which use gas burner as a source of thermal energy. We design our pipe heat exchangers for maximum waste energy recuperation efficiency. The most common application of pipe heat exchangers is combustion air pre-heating and production area heating during winter.
Heat transfer area regeneration
Industrial heat exchanger can be equipped with automatic heat transfer area regeneration using mechanic scrapers or tube rear-flushing using pulses of compressed air, all depending on the type of flue gas. The regeneration causes sediment on the heat transfer area to be periodically swept away, which guarantees stable operational conditions.
The most common applications
Flue gas heat exchangers are commonly utilized for heat exchange in foundries, melting shops, glassworks and other industries with melting aggregates with flue-gas temperatures between 300 and 700°C. Other uses include productions using direct contact with flame for heating, with higher amount of dust particles in the flue gas.
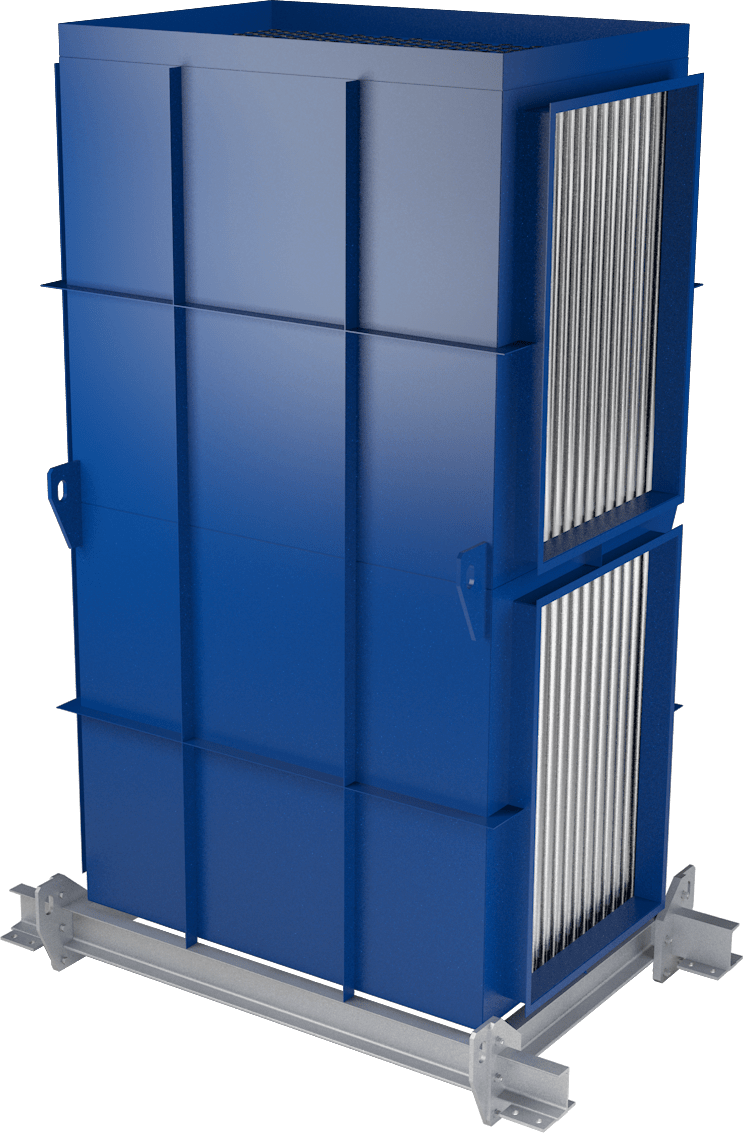
Basic characteristics
Industrial heat exchanger with automatic heat transfer area regeneration is capable of continuous flue gas heat exchange even under variable conditions such as input temperature or the volume of flue gas. Output flue-gas temperature is maintained on a preset value, which is kept above the dew point. Tube heat exchanger and integrated MaR system reduces the amount of waste thermal energy to a minimum, so condensation doesn’t take place in the heat exchanger or any attached air extraction system.
Heat exchanger power series
Due to their application in aggressive flue gas environments, pipe heat exchangers are designed exclusive in stainless steel. Based on our experience, we use heat exchangers with power from 100 kW up to 1 MW. When higher heat exchange efficiency is required, we connect several heat exchangers in series.
Flue gas heat exchange and filtration technology
Our solutions are designed as technological units, from the input filler up to the output chimney. Complex flue gas technology includes heat exchanger for utilizing waste thermal energy, sorbent feeding system for HF and HCI reduction and a filtration device for filtering PM. Installed technological unit has several safety measures to prevent damage to the filtration technology with high flue gas temperatures and to prevent productivity limitations.
We will gladly help with your design – contact us.