ABB s.r.o.
Brno / Czech Republic
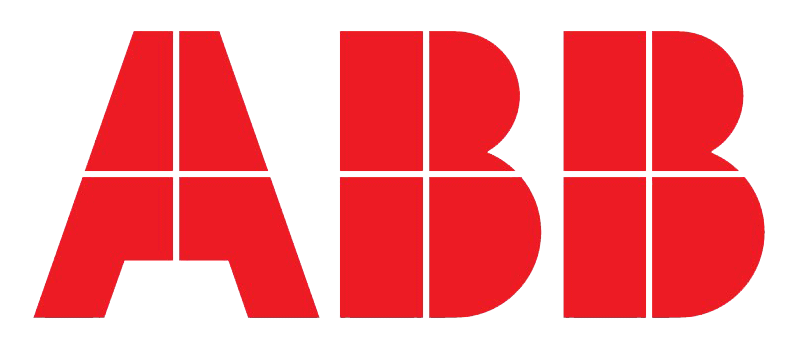
Grinding dust extraction
We deliver our technology to the world-renowned ABB company for many years. The latest technological delivery was installed in Brno’s Slatina district, where large products get ground and machined.
We approached each workplace separately when designing the extraction technology. The contract included design and complete workplace construction with extraction and filtration technology included.
Total installed exhaust power, according to the specified maximum overlapping, is 25 000 m3/h. The whole system is controlled automatically with a frequency converter and automatic dampers, which regulate exhaust power according to the availability of individual workplaces. The client appreciated the automated nature of the solution and the energy cost savings, which, with a 37.0 kW engine, are truly significant.
Extraction and filtration is carried by our CARM GH device with automatic filter medium regeneration through compressed air counterflow. Filter bags made of non-woven fabric were used as the filter medium (open filter area). In similar applications, the operating lifespan of the filter medium is usually 18 000 – 20 000 at minimum, which is positively reflected in the devices operating costs.
An absolute filter is a part of the filtration device, which keeps the filtered air purity under 0,5 mg/Nm3. During summer months, the device operates in summer mode, which means the filtered air is blown outside, and during winter months it operates in winter mode, which returns the filtered air back to the workplace. Meeting legislation limits and returning air back to the workplace significantly reduces heating costs.
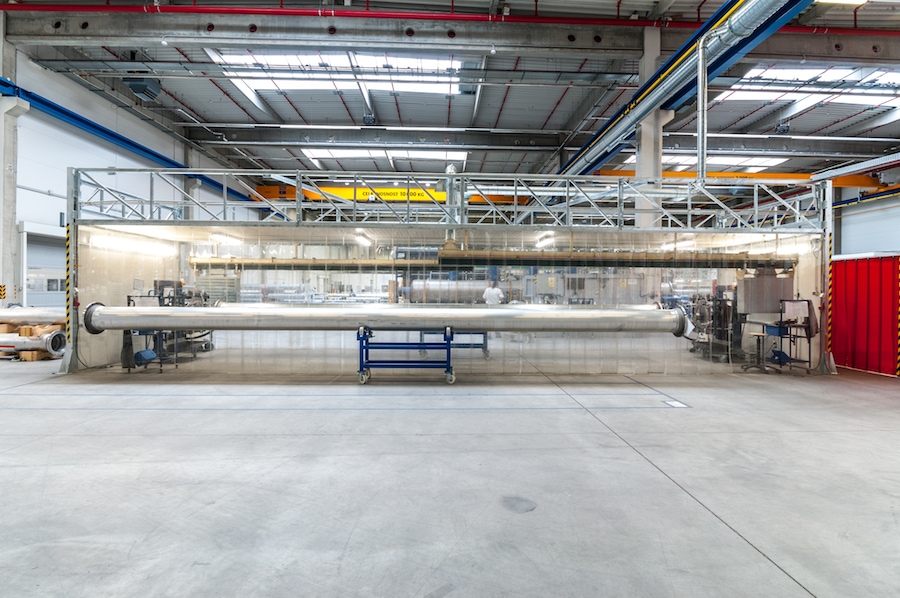
Extraction booth, grinding process, ABB s.r.o
We consulted with the client about the final design and workplace details before the production began, so each workplace would be fitted for spatial dispositions.
Specifically, seven different workplaces were part of the contract:
- Small parts grinding
- Two grinding desks with 1m long exhaust hood and a space, where coarse particles would fall down to and be stored.
- Wires and tubes grinding
- Dimensions: 14×2.5 m, with side curtain from suspended PVC strips.
- Extraction in this workplace is carried by two adjustable 3m long extraction arms together with 1.5m long exhaust hood.
- Tube grinding workplace:
- This workplace is specific for its 24x4m casing.
- Two longer and one shorter walls are made of suspended PVC strips, for entry and exit of trucks with goods.
- Wall and ceiling are made of sound-proof panels.
- Dust extraction is carried by two 1.5m sliding exhaust hoods.
- Rough tube grinding workplace:
- Workplace dimensions 14×4 m.
- Here, the two longer walls comprise of suspended PVC strips and the two shorter walls of sound-proof panels.
- Extraction technology is identical to the tube grinding workplace.
- Grinding booth:
- Stationary 1-meter long exhaust hood is part of the booth.
- The booth has two walls made of PVC strips, two walls made of sound-proof panels and sound-proof ceiling.
- Cross-cut saw:
- Extraction from the blade casing.
- Maintenance workplace:
- This workplace is dedicated to hand grinding and welding and it is covered with a stationary exhaust hood.
The result is efficient workplace air extraction and filtration.
See the finished product on the attached photos.
Ing. David Tříska